Calibration Services
Calibration of Gas Meters
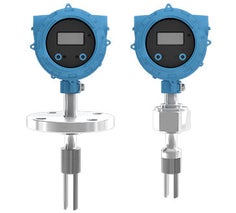
Gas detection equipment is required for ensuring spaces are safe for entry, work or other operations. Their uses include the detection of:
-
Cargo vapour in air, inert gas or the vapour of another cargo.
-
Concentrations of gas in or near the flammable range.
-
Concentrations of oxygen in inert gas, cargo vapour or enclosed spaces.
-
Toxic gases
All vessels are supplied with portable gas measuring equipment, according to the specific requirements of the vessel owners. Personnel must fully understand the purpose and limitations of vapour detection equipment, whether fixed or portable.
The importance of careful calibration cannot be over emphasised as the gas detection or analysing equipment will only give accurate readings if calibration is carried out strictly in compliance with the manufacturer’s instructions and using the correct calibration gases. Instruments must always be checked, zeroed and spanned where applicable before every use as per the manufacturer’s instructions.
Calibration may be required to be carried out ashore for some instruments. The Chief Officer is responsible for the condition monitoring and maintenance of all portable and fixed gas measuring instruments on board and ensuring sufficient span gas of the correct grade is on board. The Chief Officer is responsible for identifying, calibrating, and adjusting all portable gas measuring instruments available onboard.
Calibration of Alcohol Meters

Why does my breathalyzer need to be calibrated?
Over time, all breathalyzers, need to be calibrated. The calibration process adjusts the internal components letting the breathalyzer measures BAC (blood alcohol content) correctly, and this, at all levels detectable. If the sensor is saturated, the breathlayzer’s results may be biased. The calibration process is similar to the adjustment of a clock. When the clock is well adjusted, it displays the time precisely. By contrast, over time, the clock can lose little by little, a few minutes here and there and then eventually no longer display the correct time.
When we receive a breathalyzer for calibration, all of the following items are evaluated: battery (ies), connection wires, display, operation of the buttons, sound, mouth input / output. Following the calibration, we verify the accuracy of the results.
Calibration frequency
Your breathalyzer comes precalibrated, but it is recommended to check your device after a number of tests or months of use. Since each device is different, we recommend that you consult our FAQ or your guide for instructions in order to know the frequency of calibration for your device, since the latter may vary from 100 to 1000 tests or 6 to 1 year.
If you rarely use your breathalyzer, calibrate it once a year. The calibration process ensures that your breathalyzer is working properly and its an economical way to significantly increase the life of your breathalyzer.
Calibration of Manometer
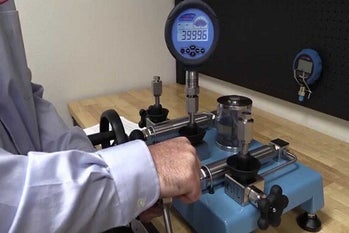
A manometer is a tool to measure pressure in closed systems. Manometers measure different types of pressure, absolute, gauge, and differential. They
generally come in two types, liquid and elastic. These types in turn divide into several models:
- U-tube manometer
- Differential U-tube manometer
- Inverted U-tube manometer
- Inclined manometer
- Bourdon pressure gauge
- Aneroid gauges
Calibration of UTI
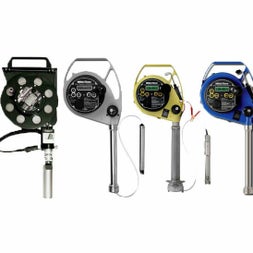
Ullage-Temperature-Interface (UTI) oil/water detector is provided for rapid and accurate determination of the oil/water interface in storage tanks. UTI detectors also advise the user of various temperatures of the monitored liquid/gas.
We provide four-range temperature testing, oil/water interface testing, calibration, repairs and replacement of inoperative parts. In most cases, same day turn-around of units is provided.
Sea Safety also conducts calibration testing of your portable temperature and pressure calibrator units.
Calibration of Temperature Sensors
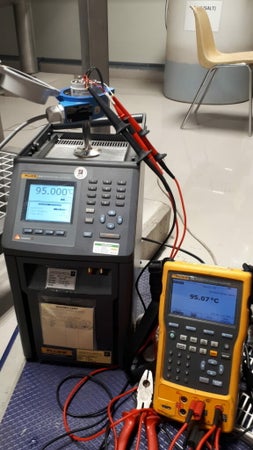
Temperature sensor calibration can be accomplished in a variety of ways and with various degrees of accuracy. As with any calibration, a standard must be used. The standards used in temperature sensor calibration can come in different forms but must be certified with an accuracy that is traceable to a national standard. In industrial applications temperature sensor calibration usually involves thermistors, thermocouples or Platinum resistance thermometers (PRTs), also called resistance temperature devices (RTDs). These are devices used to accuratly measure temperature. Readings from these devices can be compaired with less accurate field temperature sensors and used to evaluate the viability of those devices or to perform a temperature sensor calibration.
Calibration of Pressure Sensors
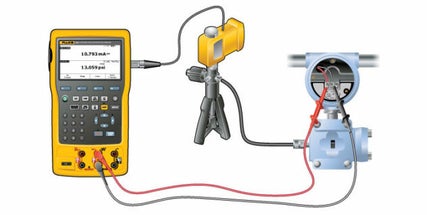
A pressure sensor is a device that changes pressure into an electrical signal. That electrical signal is only useful if it accurately represents the pressure applied to the sensor. Calibration is the process by which the sensor electrical signal is adjusted so that it has a known relationship to the applied pressure. After calibration the electrical signal can be measured and that can be used to determine the pressure at the sensor.